Dissolved Oxygen Monitor Offers ‘AutoClean’ and ‘AutoVerify’ to Reduce Sensor Fouling
The most common application for a dissolved oxygen (DO) controller is an aeration lane in a wastewater treatment plant. The harsh environments that the DO sensors operate in almost inevitably lead to sensor fouling, and sensor drift as a result. Controlling the level of dissolved oxygen in a wastewater works is essential, as the level of dissolved oxygen determines how efficiently the aerobic (oxygen dependant) bacteria break down the organic waste into inorganic byproducts. Too much oxygen is a waste of resource and energy, whereas too little, means that the bacteria struggle to survive, slowing down the disinfection process. Either way, for the plant owners it is money and time wasted.
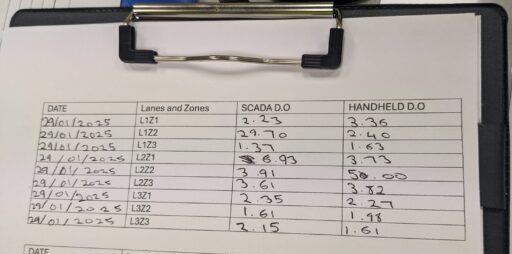
DO readings from a municipal wastewater treatment plant. ‘SCADA D.O’ refers to the submerged sensor and ‘HANDHELD D.O’ refers to the manual measurement of DO.
The image above shows data from a DO sensor on a municipal wastewater site in the UK. Each aeration lane has either one or multiple online DO sensors that are submerged in the water tanks holding the wastewater, this is the ‘SCADA D.O’. At regular intervals, the site operator goes through the plant to conduct manual tests with the ‘HANDHELD D.O’ to validate the SCADA D.O readings. In this case it is clear that the SCADA D.O is not accurately reporting the levels of dissolved oxygen as it declares a reading of 29.7 mg/l which is inconsistent with the other readings and not in line with the HANDHELD D.O reading. This anomaly could be due to drift or sensor fouling and would usually cause a signal to be sent to turn off the oxygen blowers, decreasing the true dissolved oxygen level to be below the guidelines, thus ‘killing’ the bacteria. This slows down the process of disinfection, costing time and money.
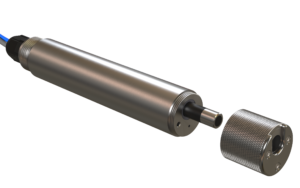
OxySense, Pi’s dissolved oxygen sensor
The solution to this is the OxySense from Pi. OxySense is a dissolved oxygen controller that is robust under harsh conditions, reliable and requires very little maintenance and calibration (up to 24 months). It is available with an ‘AutoClean’ function which reduces fouling, as the sensor is able to spray a jet of clean water or air to keep the head of the sensor free from particulate dirt. Not only this, the OxySense is the first of its kind to offer automatic in situ verification. This eradicates the need for manual testing as the OxySense can verify itself at user defined intervals and call for manual intervention only when required, saving plant operators time and reduces calibration requirements to up to 12 months, saving money for the site owners.
This site installed an OxySense and saw an almost instant difference in the consistent, reliable and accurate results when compared to the previous DO monitor that was used.
To save your operators time and yourself money, give us a call on 01282 422835 today.