Remote Access – Control InSite – CRIUS®4.0
The Process Instruments CRIUS®4.0 controller can provide as an option, remote access via LAN or GPRS modem. Utilising the IoT communications protocol, MQTT, Control InSite from Pi provides the perfect engineer’s tool in that it allows for the remote setup, diagnosis of issues and downloading of data. In fact anything you can do in front of the analyser you can do remotely from any internet enabled device.
Part of Pi’s suite of data handling products:
- Control InSite – remote access, can be used as a stand-alone remote access or alongside Data InSite®.
- Data InSite® – remote, cloud based data handling, compliance monitoring and reporting site. To see the differences between Control InSite and Data Insite®, view the videos above.
- Remote set-up – all setpoints and variables are available via the cloud based Control InSite making remote set-up, or adjustment, quick and simple.
- Remote process optimisation – sometimes a process changes and the PID control needs to be adjusted. With Control InSite, this is all done simply and quickly from anywhere in the world.
- Remote data download – collect your data remotely for analysis and interpretation.
- Remote troubleshooting – either alone or in conjunction with others, troubleshoot any issue that arises on site without travelling.
MQTT stands for Message Queuing Telemetry Transport. It is an Internet of Things communications protocol that allows small packets of data to be transferred.
Simply accessing an analyser remotely, from your desk or from another location. You can make all the changes you would make when standing in front of the analyser, but from your PC, laptop or mobile phone.
A CRIUS®4.0 controller and an internet connection. The internet connection can be via a LAN connection or 4G modem.
Any SIM card with data enabled will work.
Control InSite is Pi’s cloud based, MQTT enabled, remote access that can be used with the CRIUS®4.0 instrument controller.
Data InSite® is Pi’s online data reporting portal. The portal collects compliance data, and other data, while allowing for automatic online reporting. It is a sister product of Control InSite.
No! Control InSite is free to access when remote access hardware for the CRIUS®4.0 is purchased.
Yes. Data InSite® price plans depend on a couple of factors, the number of users and the number of data streams. It is a subscription service with pay monthly and pay annually options available.
Of course. We have a demo unit set up in our office for such reasons. Contact us and one of our sales/support team will be happy to set up a Teams or Zoom call to show you how it works.
As per the MQTT communications protocol, the data is encrypted meaning it is as secure as it can be.
With some industry standard MQTT integration, this would be possible.
Yes, although it is best if the data is imported as HTML, MQTT, .csv or added manually. If your data is in another format, please contact us to discuss.
Focus Ons are a series of short articles distributed by email providing technical information regarding instrumentation, process measurement in potable, waste, process and pool waters. If you would like to join the mailing list, please contact us.
You probably know that Process Instruments offers a cloud based remote access service for our CRIUS®4.0 analyser, but did you know that…
…nearly everything you can do in front of the analyser you can do remotely?
…the CRIUS®4.0 is the first analyser in the world to utilise MQTT, allowing for real time data without a delay?
…customers have seen the number of engineer callouts drastically reduce, saving them time and money?
…Control InSite has been allowing engineers to access CRIUS®4.0 remotely, keeping them safe during COVID?
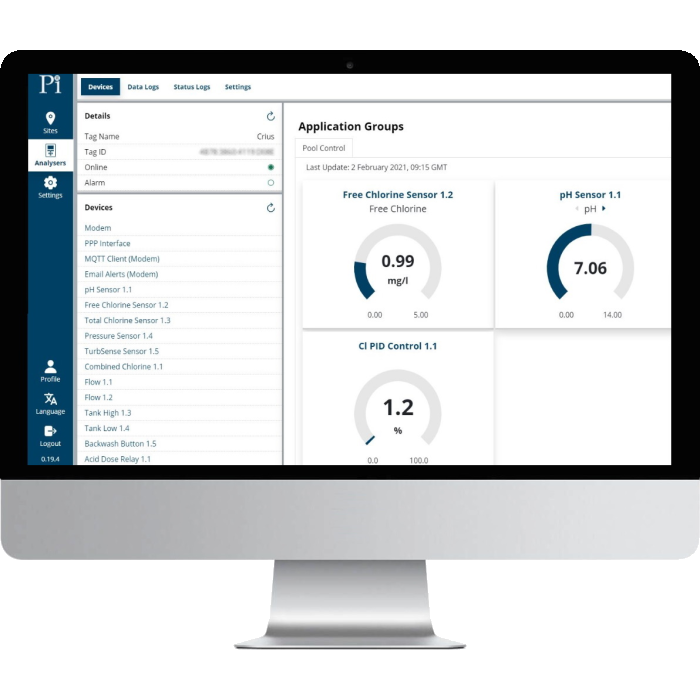
Pi’s sleek and modern remote access solution Control InSite now utilises MQTT (an Internet of Things communications protocol)
Pi has always been a leader in developing new technology and have had a remote access system for over 15 years! The latest iteration of remote access, is called Control InSite and is now a key part of our solution toolbox. Here are some of the features of our remote access:
User interface – A modern and intuitive user interface makes using Control InSite simple. Anyone requiring training can now be trained remotely using remote access and Teams or Zoom.
Speed – The service now runs around 50 times faster than its predecessors, allowing users to connect and download the current sensor values and settings in under 30 seconds (test performed on a CoagSense coagulation controller with 27 different devices such as sensors!).
Reduced data costs – By making the connection between the server and analyser more efficient, Pi has reduced the amount of data required for nearly all tasks thereby significantly reducing costs.
SIM card – By utilising IoT protocols, CRIUS®4.0 remote access can use any data enabled SIM card.
Customer branding – On request, Pi can brand the remote access theme to promote a customer’s brand.
Data analysis – The graphical interface is a powerful and flexible tool for viewing your sensor data. The way we handle your analyser’s data means that every single data point is stored in the cloud, allowing a user to download 3 months’ worth of data with a single click.
Email and text alarms – Direct from the server, cheap and reliable to up to 5 SMS recipients and 5 email recipients.
Data limit – Users can now limit how much data each analyser can use per day, meaning no unexpected data costs.
So what can Control InSite do for you?
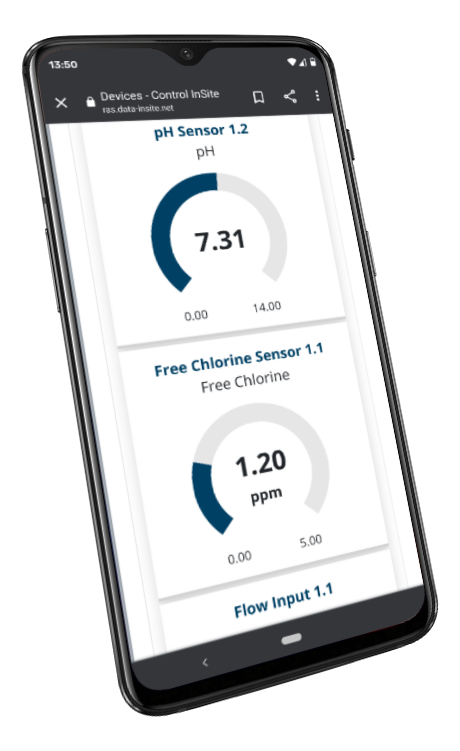
The remote access service has always been designed to save you time and money by allowing you access to the analyser and its data from anywhere in the world. Now remote access can assist as a tool in doing a lot more:
- Remotely checking and changing settings for customers who may not be confident in doing so or who may not have access to the analyser.
- Allowing Pi’s service team to temporarily remotely connect to the analyser if customers have an issue and are unsure about how to solve it.
- Easily view when maintenance is required or due on analysers, allowing users to efficiently plan which sites to visit and when.
- Know when alarms activate on the unit within seconds by enabling text and/or email alerts direct from the analyser.
- Tune control values to optimize dosing without the need to visit the site.
- Analyse stored data to investigate incidents, explain issues or validate the process.
- Save money by reducing the number of callouts and the number of miles your engineers travel!
But what about security?
MQTT is an encrypted ‘internet of things’ communications protocol designed to provide excellent security, so no worries there.
How does user access work?
Each user has their own username and password. This means that what they see and what they can do can be customised so only authorised users can make changes.
Conclusion
Using MQTT means that communication with the CRIUS®4.0 is quick, inexpensive, reliable and secure. The frequency of communication that MQTT allows means that the data you are looking at is effectively live. The size of the packets means that there is no increased data overhead so the costs are effectively the same or lower than other communications protocols that can’t provide live data.
The way the communications works is that the CRIUS®4.0 is in communication to a cloud based ‘broker’. It is then possible for other cloud based services to ‘subscribe’ to the data of that CRIUS®4.0. This means that at the same time the CRIUS®4.0 is talking to Control InSite, it can be talking to a data storage and reporting portal like Data InSite® from Pi or another proprietary portal.
Control InSite is cloud based meaning it is accessible from any internet enabled device anywhere in the world, meaning you can access it without even getting into your car or standing in front of the analyser. This feature is one of the biggest advantages of Control InSite and has been particularly useful during COVID, a time when reducing the number of site visits has been of utmost importance.
You’ve probably heard the phrases ‘Water 4.0’, ‘Industry 4.0’, ‘Internet of Things’ and ‘SMART and DIGITAL’ but did you know that…
…Pi’s CRIUS®4.0 controller was launched with a new remote access platform (the first controller in the world to use MQTT)?
…Pi already has SMART and DIGITAL installations all over the world?
…Pi works as partners to many multinational organisations to provide their remote access, remote comms and SMART technology?
CRIUS®4.0 vs CRIUS® – what’s the difference?
The CRIUS® instrument controller has been upgraded to include the IoT communications package MQTT (Message Queuing Telemetry Transport) and launched in January 2021. All CRIUS® will be CRIUS®4.0 from 1st February 2021 unless by prior arrangement with Pi.
What does MQTT mean to me?
LIVE DATA! MQTT allows very small packets of data to be sent very frequently, which means that when you log on to a CRIUS®4.0 the data you see is updated effectively live. Lots of other things are easier using MQTT. Taking advantage of these means that with CRIUS®4.0…
- Any data-enabled SIM card works with our modems
- Emails and SMS alarms are much cheaper than before
- Much easier to connect to a LAN (Local Area Network)
- Security is enhanced with encrypted data
- The ‘service’ file which details the configuration of the CRIUS®4.0 is readable and downloadable remotely
- Connection to others’ data portals provides REAL TIME, LIVE DATA.
So what is Industry 4.0 (and Water 4.0 and the Internet of Things and SMART and DIGITAL technology)?
Simply put the concept is that we are currently living through the 4th Industrial Revolution.
The first was mechanisation, (what we currently think of as the Industrial Revolution), so steam engines, Spinning Jennies, railways, canals and factories in the 1800s.
The second was the age of mass production so; electricity, the production line, etc., largely in the first half of the 20th century.
The third was computers and automation, in the latter part of the 20th century, and the fourth?
The fourth (Industry 4.0) is about ‘SMART’ factories. (The original use of the expression Industry 4.0 was by a group of advisers to the German government who presented their advice in 2012). Industry 4.0 is about making factories as SMART as they can be. That is having assets (machines, people, robots, AI, cyber technology etc.) all communicating with each other.
The main principles put forward were based on;
- Interoperability – everything should be able to talk to everything else.
- Information Transparency – the physical world should be able to be recreated virtually to allow for testing and modelling.
- Technical Assistance – information should be presented in a way that supports people to make good and fast decisions.
- Decentralisation – after decades of centralisation to things like DCS systems and SCADA systems, the future is to enable as many decisions as possible to be made locally by whatever intelligence (human or machine) is available.
So what is Water 4.0 and SMART and DIGITAL?
Water 4.0 is simply how this technology and philosophy will be implemented/will affect the water industry. There are some clear outcomes from the above… more sensors… more modelling… ‘SMARTER’ instruments, controllers, pumps etc…
SMART and DIGITAL as terms aren’t quite as well defined as others. Generally it is accepted that SMART is the increasing sophistication of equipment to make decentralised decisions. For example, in 1990 a chlorine analyser measured chlorine in water, gave out a 4-20mA output proportional to the chlorine and a couple of relays.
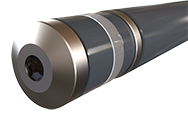
Now the CRIUS® HaloSense (fully Water 4.0 developed) can provide the 4-20mA output and the relays, but also has multiple digital comms options (INTEROPERABILITY), has space for up to 16 sensors (INFORMATION TRANSPARENCY), has wireless and wired internet access (TECHNICAL ASSISTANCE) and full PID capability with remote setpoint, i.e. another device can set the setpoint (DECENTRALISATION). So SMART technology is the technology that allows for the implementation of Industry 4.0 or Water 4.0. DIGITAL tends to refer to the comms capability.
So what is the Internet of Things or IoT?
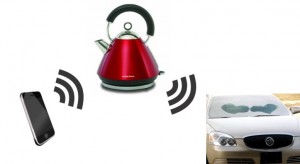
When the previous Industrial Revolutions happened, the technology and concepts spilled over into the consumer world from the business/manufacturing world. With Industry 4.0 it is beginning to be the other way around with consumer demand for the internet, and mobile phone technology, driving the technology. If we assume that in this Industrial Revolution the same thing will happen, then the Internet of Things refers to all devices we use all the time talking to each other and making their own decisions.
Imagine your mobile phone waking you at 6am and telling your kettle that turns itself on at 6.20am, which tells your car that starts itself and defrosts the windscreen at 6.30am etc…
Not convinced that we are in a new Industrial Revolution?
Consider this… perhaps Industrial Revolutions are only identifiable in hindsight?
And what does it matter? Well from Process Instruments’ point of view, it doesn’t. As long as our products are leading the way in providing our customers with what they need to enable their own Industry 4.0, and Pi is leading the way with the world’s first MQTT enabled instrument controller.
Document | Type | Size |
---|---|---|
Remote Access – InSite | Brochure | 1.3mB |
Remote Access – LIVE DATA | Technical Note | 586kB |
CRIUS®4.0 | Brochure | 860kB |
Water 4.0, Industry 4.0, IoT, SMART and DIGITAL | Technical Note | 727kB |
"We at Scottish Water have been using the excellent Pi LabSense 3 and portable UV254 instruments in the field for optimizing our Water Treatment processes for some years now. We find them easy to use and invaluable for detecting and resolving issues in a timely, efficient and effective manner. Two great pieces of kit!”
Paul Weir
Scottish Water - UK
"I want to thank you and all at Process Instruments for all the assistance, information and handholding during the year. The help that was so freely given was very much appreciated. Can you please extend my appreciation to all at Pi and let me wish you all a happy, safe and wonderful Christmas and I look forward to working with you again in 2021."
Michael Bailey
Wexford Co. Co. - Ireland
"Excellent level of support and always so much more prompt than a lot of our suppliers."
Phill Tuxford
Detectronic - UK
"The plant can’t produce good quality water without the CoagSense."
Mick Murphy
Wexford Co. Co. - Ireland
"We started using Process Instruments 10 years ago and they worked so well that when we were looking at expanding, Process Instruments were our "go to" company."
Rebecca - Pool Manager
Woodland Spa - Burnley, UK
"We've been installing pools and spa controllers from Pi for more than 10 years and they just are the best on the market."
Dr. Lester Symmonds
Pool Sentry - UK
"We've used the CRIUS® with chlorine, pH and conductivity sensors for several years and confirm quality, performance and reliability has been wholly satisfactory to date."
David Kerr
Karis Technical Services Ltd. - UK
"We in ECM ECO Monitoring can only recommend Process Instruments products and services to all other potential clients. They have very complex portfolio of products for water quality monitoring in various types of industries, friendly attitude, very quick delivery time and prompt reaction to all our needs and inquires. Our clients especially appreciate the particle counters and sizers allowing identification of drinking water treatment problems. The Streaming Current Monitors are a great tool for optimisation of expensive chemicals.”
Branislav
ECM ECO Monitoring - Slovakia
"Simply the best turbidity available."
John Clark
Chemtrac - Atlanta, GA
"In 2019, we purchased 29 particle counters which were installed in our water plants. So far, their performance has been perfect."
Li Yongjun
Jinan Hongquan Water Company - China
"We have installed hundreds of ozone analyzers from Pi over the years. They are just accurate, reliable and require low maintenance."
Jiao Tumei
Qingdao Guolin Environmental Technology Co., Ltd., - China
"Over the last few years we've purchased chlorine and turbidity analyzers from Chemtrac and with routine calibration the probes measure the chlorine and turbidity without any issue. We are very happy with this product and would highly recommend them."
Daniel "Buck" Owen
Ocoee Utility District - Ocoee TN
"We've been using these analyzers since 2008. They're easy to use and very stable. Calibration and maintenance is quick and simple."
Lloyd Gruginski
Chehalis WTP - Chehalis, WA
"The Pi products provide excellent value for money and represent the best municipal drinking water analyzers available."
John Clark
Chemtrac - Atlanta
“Servicing customers is much more than just solving problems or addressing complaints and Pi does that very competently with technical and quick efforts providing a good experience."
Clovis Tuchapski
Buckman - Latin America
"Pi's technical team has enabled us to be one step ahead of our competitors by adding value to our projects thanks to their fast and excellent support from the moment you first reach out.
Ibrahim Kaplin
Thermomed - Turkey
"Going from ORP control to amperometric chlorine sensor control has undoubtedly improved the pool water immensely!"
Chris Tedeschi
Link Automation - USA
"The Streaming Current Monitor from Pi is the best SCM I have ever used. The analyser responds quickly and has many powerful functions, which helps me save a lot of money."
Ye Yancong
Xiamen Xishan Water Plant - China
“Process Instruments has a broad range of high quality and user-friendly solutions for water-industry problems. The short lead times and great customer support make Pi a reliable partner.”
Péter Szabó
SC KATALIN NOHSE CHIMIST IMPORT SRL - Romania
"Process Instruments UK always have a high level of customer service. All our interactions with Pi have exceeded our expectations. It is always a pleasure working with you.”
Iñaki Seisdedos Rodríguez
Izasa Scientific - Spain
"The support from Pi and its partners is superb. They go above and beyond to ensure that, not only is their equipment perfect but that the process is working great too. Five Stars!"
Anthony Glitto
Equip Solutions - Illinois, USA
"Process Instruments UK always have a high level of customer service. All our interactions with Pi have exceeded our expectations. It is always a pleasure working with you.”
Rudi Tuffek
Allpronix - South Africa