DO Meter - Dissolved Oxygen Meter – OxySense
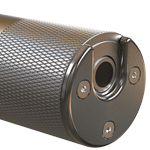
Dissolved Oxygen Sensor – OxySense S
The OxySense DO meter range of online Dissolved Oxygen Meters utilises the very latest and best optical sensor available in the world today. It is an optical luminescent device which is extremely resistant to abrasion, extremely stable, and has greatly reduced maintenance and whole life costs. Coupled with the automatic self-cleaning and self-verification, the OxySense online DO meter is as close to ‘fit and forget’ as it gets.
The OxySense Online Optical DO meter with self-cleaning and self-verification offers enhanced reliability and unrivalled low maintenance. Optical DO sensors have largely replaced electrochemical DO sensors (Clark Cells) due to their better reliability and lower maintenance requirements.
The OxySense DO sensor is available with different controllers giving you the same great performance with different communication, display, and control options.
The sensing element (lumiphore) is activated, or excited when illuminated with a blue light. When activated, the lumiphore then emits red light with an intensity that is inversely proportional to the amount of oxygen dissolved in the water.
There is also a time delay between the peak emission of blue light and peak response of fluoresced red light. The amount of delay is inversely proportional to the amount of oxygen present. This time delay can be expressed as a phase shift between the wave patterns of incident blue light and the fluoresced red light. This is in turn reported by the DO meter electronics as a ppm or mg/l reading of dissolved oxygen. The advantages of this technology are that it is more stable than traditional electrochemical devices and far more resistant to abrasion. By using the state of the art sensor and electronics together the reliability, accuracy, and flexibility of the OxySense Online Optical DO meter is far superior to that of its competitors. great value for money.
The OxySense DO meter is used in aeration lanes and oxidation ditches to control the air blowers. What is probably the world’s most reliable dissolved oxygen sensor coupled with Pi’s award winning electronics provides up to 24 months between maintenance and calibration events and results in probably the best online DO meter available in the world today.
The self-verification option is revolutionising calibration routines in that this Dissolved Oxygen analyser is able to check its own functionality on a regular basis and call for calibration when necessary.
- Down to zero maintenance
- No chemicals or moving parts
- Optional self-cleaning and self-verification system
- Stable and reliable – excellent process control
- Suitable for all Dissolved Oxygen applications
- Up to 24 months between maintenance
- No initial calibration required
- Rugged online optical DO meter
- Better performance than competitors’ dissolved oxygen sensors
- Range of process control PID options – reducing labour costs
- Optional AutoFlush Compressor
- Proven reliability
- Up to 24 months between calibration events
- Data-logging and remote internet access with text alarms
The online measurement of Dissolved Oxygen in an aeration lane or an oxidation ditch is critical to the efficient running of the plant. With the electrical costs of aerating the waste water with blowers etc. often making up 50% of the total running costs of the plant, any drift or inaccuracy of the measurement can result in large sums wasted.
This reliance on online DO meters to control the blowers etc. means that they must be reliable, robust and free of drift; in an ideal world they would be free from maintenance, an ongoing, tedious, and expensive aspect of owning dissolved oxygen analysers.
The general industry move away from amperometric Clark cells towards optical sensors has made a large improvement to monitoring DO in aeration lanes, but not all optical DO meters are the same. Many, even the industry leaders, drift over time and are subject to high levels of maintenance.
Pi has created an instrument designed to give the industry as close to a zero maintenance instrument as possible.
- Lumiphore life of 2 years plus
- Extremely low drift
- Autoclean – water or air
- Alarms for dirty sensor, lack of response, sensor failure etc.
- No initial calibration required
- Zero operator intervention for up to 2 years
In a trial in the UK, an OxySense DO meter was installed on an aeration lane and required zero maintenance (including calibration) for over 12 months whilst maintaining its accuracy.
If you would like to run a trial in your plant or would like to learn more about the OxySense DO meter from Pi then why not contact us?
The OxySense S is designed specifically for dipping into aeration lanes or oxidation ditches. It is fully waterproof and comes with self cleaning as standard.
As described elsewhere, the OxySense can come equipped to automatically clean itself at user defined intervals with all the benefits of no operator intervention. The AutoFlush is particularly useful in food preparation, pulp and paper, and many applications where there is likely to be a build up of solids in the sample.
The whole range of OxySense meters can be fitted with additional sensors such as chlorine or pH. Please ask your local distributor for more details.
It is probably the most reliable and cost effective DO sensor available as it;
- is extremely resistant making it last longer in the harsh environment of an aeration lane.
- can self clean and self check its response every time it cleans.
Pi has developed a special end cap that screws onto the end of the sensor. It is smooth and low profile to reduce the possibility of ragging. An air blast cuts across the flat sensor end helping it clean.
When the sensor is being cleaned the design of the end cap means that the water is excluded from the end cap by the force and volume of air. This cleans the end cap (lumiphore) and exposes the sensor to air. The sensor then reads the DO in air (which is much greater than in water) and that response is measured. If the response is not what is expected an error is flagged for the operator to intervene.
How often and for how long the sensor is cleaned is set on the simple controls on the analyser itself. It is also possible to set a ‘hold’ for the output from the analyser to ensure that the control is not affected by the self clean. This ‘hold’ starts at the beginning of the cleaning cycle and continues for a user defined time after the cleaning cycle.
That depends on the process but two years is typical.
Yes very! You just unscrew the old one and scew on the new one. No need to enter anything on the analyser.
Yes, a clean pressurised water supply can be used instead of compressed air to clean the sensor, however the self verification function would not work if water is used to clean the sensor.
No, there are no moving parts beneath the water. All moving parts are easily accessible.
Measuring dissolved oxygen in water can be done using a variety of methods. Online these are generally of two types, “electrochemical” and the later type “optical”. There are variations within these two groups but fundamentally the electrochemical sensors measure the rate of an electrochemical reaction that is changed by the presence of oxygen and the optical devices measure the amount of light of a particular wavelength that is given out by an optically sensitive material that is also influenced by the amount of oxygen dissolved in water. The advantage of the optical devices is that they require less maintenance, but they are more expensive.
Dissolved oxygen in water is normallly measured with a “hand-held” device or with a continuous online analyser such as the OxySense from Pi.
The organisms in water require dissolved oxygen in order to live. If the levels get too low then the organisms in the water will die. People involved with the environment use dissolved oxygen measurements to determine the “health” of the water.
In wastewater treatment, dissolved oxygen is introduced into the waste water in an oxidation ditch or aeration lane in order to support the life of the micro-organisms that digest and render harmless our waste. By measuring the dissolved oxygen online operators can balance the activity of the organisms in the wastewater with the cost of the blowers.
Oxygen is introduced to water through plant photosynthesis in the aquatic plants, or though the dissolution of oxygen from the air. The total amount of dissolved oxygen in water varies but is generally between 6.5 mg/L (ppm) and 8.5 mg/L (ppm). The warmer the water is, the less oxygen can be dissolved in the water and the more polluted the water is the less dissolved oxygen will be present.
Focus Ons are a series of short articles distributed by email providing technical information regarding instrumentation, process measurement in potable, waste, process and pool waters. If you would like to join the mailing list, please contact us.
Sensor Fouling
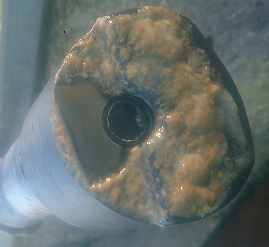
What is the solution?
Process Instruments’ AutoClean and AutoFlush Systems
Simple, reliable and easy to maintain, Process Instruments’ AutoClean/AutoFlush systems are an alternative to mechanical cleaning mechanisms which can clog and break. By frequently spraying the sensor/probe with clean water or air, the sensor remains clean and free from fouling for extended periods of time. The sensor cleaning cycle is activated by Pi’s controller for a user selectable length of time and frequency so that no matter how dirty the application, the probe remains clean. With no moving parts in the sensor body or in the cleaning attachment there is nothing to replace or check other than a simple valve positioned in an easy to reach location.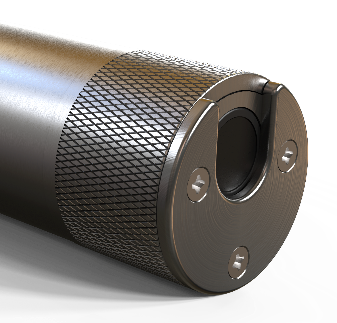
A solution for each application
AutoClean
This option can be added to our pH, ORP, Turbidity, Suspended Solids and Dissolved Oxygen (DO) sensors. Consisting of an end cap to direct the flow of clean water (or air for a DO sensor) across the face of the sensor blasting any dirt away. The cleaning is controlled by a single valve positioned in an easily accessible location.AutoVerify
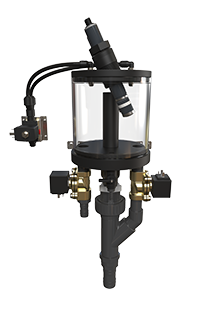
AutoFlush
For sensors that require flow cell mounting like Chlorine, Ozone and Chlorine Dioxide, an Autoflush system has inbuilt valves which automatically start/stop the sample flow and control the flow of clean water past the probe. The user can set the flushing interval and duration to keep the flow cell and sensor clear from fouling. For particularly dirty or stubborn contaminants, warm water can be used as the flush water to aid cleaning. With the above options, whatever the application or parameter being measured, Process Instruments will be able to provide a monitoring system that will not only be accurate, precise and long lasting but that will also remain free from fouling and save the operator both time and money.You probably know that online dissolved oxygen monitors are crucial for controlling the oxygen available to the microbes in an aeration lane or oxidation ditch but did you know that…
…typically up to 50% of the cost of running a waste water treatment plant with aeration is the cost of the electricity to run the blowers?
…often the cost of purchasing many online DO meters is less than 10% of its 10 year total cost of ownership?
…an online DO meter that is reading 0.1ppm low could cost more than its purchase and installation costs in increased electricity costs in just a few months?
Galvanic vs Optical DO measurements
Early measurement of online dissolved oxygen in waste water was made by electrochemical cells that needed sacrificial electrodes, electrolyte, membranes and a lot of calibration. Whilst there are some companies still advocating the use of this technology it was largely replaced in the 1990s and 2000s with online optical measurement. The vast majority of online DO systems used today are optically based.
Why is controlling the blowers so important?
Simply put, the microbes need enough oxygen to do the job. More oxygen than this, and we are wasting energy and promoting the growth of unwanted biologies in the process. Many plants are estimated to waste significant energy by over aerating their process.
What do you need from an online DO meter?
Reliability, Dependability and Reproducibility are the three most important things that a plant needs if it is to optimise its treatment (i.e. control the DO in the aeration lanes to a precise and accurate level).
Typically, an aeration basin will have ‘lanes’ with more than one DO sensor. If these DO meters are reading very different levels and do not track each other it is very difficult for a plant to know how to implement a control strategy. DO meters fail low, an unfortunate consequence of the technology. A reliable, dependable and reproducible DO meter will be consistent and will check its own responsiveness so an operator doesn’t need to worry.
Reliability means Robust
The Process Instruments sensor has what is probably the most robust lumiphore (sensing material) of any available DO meter. The lumiphore is the disc of material that is used to sense the amount of oxygen present and it needs to be tough to withstand the high energy, aggressive environment that they work in.
Dependability means Clean
If you ask operators how often they maintain a DO meter (clean/calibrate etc.) you often get the answer “every week”. On a large plant that can mean an operator spends half their time doing nothing but maintaining the DO sensors!
The Pi online DO analyser has an optional cleaning system that can clean the lumiphore and keep it clean potentially for the entire life of the sensor. Utilising compressed air from site or a small robust compressor available from Pi, the Autoclean keeps the sensor clean and that’s not all…
Dependability means Self-Checking
If you ask the operator why they clean/calibrate the sensor weekly you will often get the answer “so we know it’s working”.
In modern plants the DO levels are kept low to reduce the energy required for the blowers. This means that the DO sensors can often read close to 0mg/l.
How do we know that the sensors are reading correctly and aren’t faulty?
The traditional solution is for an operator to pull the sensor out and watch it respond to air, and when it’s out the operator may as well clean it and calibrate it.
What if there was a way to check the response to air without taking it out of the aeration lane?
Well there is! The Pi Autoclean system not only automatically cleans the system but whilst doing so, also checks the response to air. Any issues are reported to the operator who no longer has to maintain the sensors every week.
How long can they last without any operator interference?
On a recent trial in a UK Utility the Pi OxySense was installed for 13 months alongside their existing dissolved oxygen analyser and during that time the sensor was removed once for manual cleaning when the power to the Autoclean system was inadvertently off for a week. That was the only time the sensor was removed from its position in the aeration lane and throughout the entire trial the instrument was reliable, dependable, and consistently accurate.
Sensor Fouling
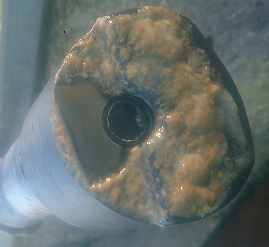
What is the solution?
Process Instruments’ AutoClean and AutoFlush Systems
Simple, reliable and easy to maintain, Process Instruments’ AutoClean/AutoFlush systems are an alternative to mechanical cleaning mechanisms which can clog and break. By frequently spraying the sensor/probe with clean water or air, the sensor remains clean and free from fouling for extended periods of time. The sensor cleaning cycle is activated by Pi’s controller for a user selectable length of time and frequency so that no matter how dirty the application, the probe remains clean. With no moving parts in the sensor body or in the cleaning attachment there is nothing to replace or check other than a simple valve positioned in an easy to reach location.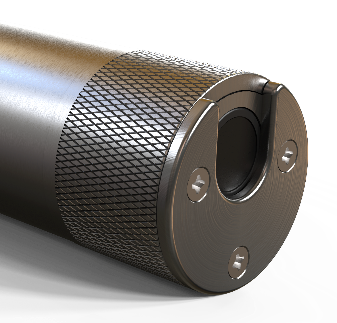
A solution for each application
AutoClean
This option can be added to our pH, ORP, Turbidity, Suspended Solids and Dissolved Oxygen (DO) sensors. Consisting of an end cap to direct the flow of clean water (or air for a DO sensor) across the face of the sensor blasting any dirt away. The cleaning is controlled by a single valve positioned in an easily accessible location.AutoVerify
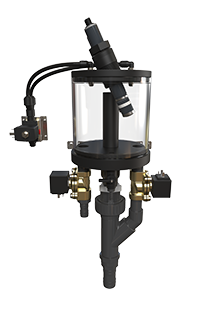
AutoFlush
For sensors that require flow cell mounting like Chlorine, Ozone and Chlorine Dioxide, an Autoflush system has inbuilt valves which automatically start/stop the sample flow and control the flow of clean water past the probe. The user can set the flushing interval and duration to keep the flow cell and sensor clear from fouling. For particularly dirty or stubborn contaminants, warm water can be used as the flush water to aid cleaning. With the above options, whatever the application or parameter being measured, Process Instruments will be able to provide a monitoring system that will not only be accurate, precise and long lasting but that will also remain free from fouling and save the operator both time and money.Introduction
Northern Ireland Water (NIW) recently trialled three dissolved oxygen analysers (DO meters) in parallel. These were installed at Culmor Waste Water Treatment Plant side by side in the same aeration lane, where measurements were recorded every minute for 6 months.
After processing more than a million points of data, the OxySense from Process Instruments (Pi) was shown by NIW to be the best solution.
The graph shows a three hour snapshot of some of the results that led to NIW deciding that Pi’s DO meter performed the best overall. From looking at this graph it is clear why Pi was preferred: Competitor A’s sensor displays a low, inaccurate reading and Competitor B’s sensor is afflicted by noise. These results are discussed in more details later in this Focus On.
The Plant
The trial plant had used Competitor B’s DO meters for some time in all their aeration lanes, however they found that the sensing end cap required replacing quite frequently (every 6 months). The replacement costs of £90 ($120, €105) per sensor started to accumulate and the plant decided to seek an alternative.
Auto-Cleaning
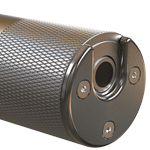
Dissolved Oxygen Sensor – OxySense S
Pi’s sensor was equipped with its Autoclean end cap (see image, right), which actively cleans the sensor with compressed air (or clean water) to remove sludge and debris from the sensor tip on a regular basis.
Peter Martin, M&E Manager, NIW.
Competitor A’s sensor was attached to a flexible mounting which allowed the sensor to move with the sludge and aeration bubbles, theoretically cleaning the sensor passively.
Competitor B’s sensor did not have any automatic cleaning functionality.
All three sensors periodically received a manual clean as part of the plant’s regular maintenance schedule, ensuring the test was fair for the sensors without a cleaning system.
Results
Measurements from the 25th of May 2015 have been used to demonstrate the variation between the different analysers. This date set was chosen to be representative of the whole trial.
Process Instruments
The trial found that the CRIUS® OxySense from Pi provided the most accurate and reliable DO meter. The sensor was kept clean by Pi’s Autoclean system, and reported accurate and precise readings with the lowest noise. A gradual increase in dissolved oxygen content is easily observed during aeration, followed by a steady decline as the air blowers are turned off.
Competitor A
Competitor A’s sensor struggled to keep itself clean between the regular maintenance events, as the passive self cleaning system was ineffective. The instrument appears to inaccurately report lower readings as a result of sludge and debris coating the sensor. The DO sensor detects the increased oxygen dissolved during aeration, but then falls to a reading of zero for long periods of time.
Competitor B
Readings from Competitor B’s sensor appear to lack precision and contain noise. This is most likely due to fouling of the sensor head (see image, right). The results had large variations between measurements, often making it difficult to distinguish the peaks during aeration. By the end of the six months, Competitor B’s sensor was found to be worn and required a replacement lumiphore end cap.
Peter Martin, M&E Manager, NIW.
You probably know that online dissolved oxygen monitors are crucial for controlling the oxygen available to the microbes in an aeration lane or oxidation ditch but did you know that…
…typically up to 50% of the cost of running a waste water treatment plant with aeration is the cost of the electricity to run the blowers?
…often the cost of purchasing many online DO meters is less than 10% of its 10 year total cost of ownership?
…an online DO meter that is reading 0.1ppm low could cost more than its purchase and installation costs in increased electricity costs in just a few months?
Galvanic vs Optical DO measurements
Early measurement of online dissolved oxygen in waste water was made by electrochemical cells that needed sacrificial electrodes, electrolyte, membranes and a lot of calibration. Whilst there are some companies still advocating the use of this technology it was largely replaced in the 1990s and 2000s with online optical measurement. The vast majority of online DO systems used today are optically based.
Why is controlling the blowers so important?
Simply put, the microbes need enough oxygen to do the job. More oxygen than this, and we are wasting energy and promoting the growth of unwanted biologies in the process. Many plants are estimated to waste significant energy by over aerating their process.
What do you need from an online DO meter?
Reliability, Dependability and Reproducibility are the three most important things that a plant needs if it is to optimise its treatment (i.e. control the DO in the aeration lanes to a precise and accurate level).
Typically, an aeration basin will have ‘lanes’ with more than one DO sensor. If these DO meters are reading very different levels and do not track each other it is very difficult for a plant to know how to implement a control strategy. DO meters fail low, an unfortunate consequence of the technology. A reliable, dependable and reproducible DO meter will be consistent and will check its own responsiveness so an operator doesn’t need to worry.
Reliability means Robust
The Process Instruments sensor has what is probably the most robust lumiphore (sensing material) of any available DO meter. The lumiphore is the disc of material that is used to sense the amount of oxygen present and it needs to be tough to withstand the high energy, aggressive environment that they work in.
Dependability means Clean
If you ask operators how often they maintain a DO meter (clean/calibrate etc.) you often get the answer “every week”. On a large plant that can mean an operator spends half their time doing nothing but maintaining the DO sensors!
The Pi online DO analyser has an optional cleaning system that can clean the lumiphore and keep it clean potentially for the entire life of the sensor. Utilising compressed air from site or a small robust compressor available from Pi, the Autoclean keeps the sensor clean and that’s not all…
Dependability means Self-Checking
If you ask the operator why they clean/calibrate the sensor weekly you will often get the answer “so we know it’s working”.
In modern plants the DO levels are kept low to reduce the energy required for the blowers. This means that the DO sensors can often read close to 0mg/l.
How do we know that the sensors are reading correctly and aren’t faulty?
The traditional solution is for an operator to pull the sensor out and watch it respond to air, and when it’s out the operator may as well clean it and calibrate it.
What if there was a way to check the response to air without taking it out of the aeration lane?
Well there is! The Pi Autoclean system not only automatically cleans the system but whilst doing so, also checks the response to air. Any issues are reported to the operator who no longer has to maintain the sensors every week.
How long can they last without any operator interference?
On a recent trial in a UK Utility the Pi OxySense was installed for 13 months alongside their existing dissolved oxygen analyser and during that time the sensor was removed once for manual cleaning when the power to the Autoclean system was inadvertently off for a week. That was the only time the sensor was removed from its position in the aeration lane and throughout the entire trial the instrument was reliable, dependable, and consistently accurate.
Document | Type | Size |
---|---|---|
OxySense | Brochure | 848kb |
NIW DO Trial | Article | 1.2mB |
Dissolved Oxygen Meter for Aeration Control | Technical Note | 602kB |
AirFlush | Technical Note | 594kB |
Probe Fouling | Technical Note | 459kB |
"We at Scottish Water have been using the excellent Pi LabSense 3 and portable UV254 instruments in the field for optimizing our Water Treatment processes for some years now. We find them easy to use and invaluable for detecting and resolving issues in a timely, efficient and effective manner. Two great pieces of kit!”
Paul Weir
Scottish Water - UK
"I want to thank you and all at Process Instruments for all the assistance, information and handholding during the year. The help that was so freely given was very much appreciated. Can you please extend my appreciation to all at Pi and let me wish you all a happy, safe and wonderful Christmas and I look forward to working with you again in 2021."
Michael Bailey
Wexford Co. Co. - Ireland
"Excellent level of support and always so much more prompt than a lot of our suppliers."
Phill Tuxford
Detectronic - UK
"The plant can’t produce good quality water without the CoagSense."
Mick Murphy
Wexford Co. Co. - Ireland
"We've used the CRIUS® with chlorine, pH and conductivity sensors for several years and confirm quality, performance and reliability has been wholly satisfactory to date."
David Kerr
Karis Technical Services Ltd. - UK
"We in ECM ECO Monitoring can only recommend Process Instruments products and services to all other potential clients. They have very complex portfolio of products for water quality monitoring in various types of industries, friendly attitude, very quick delivery time and prompt reaction to all our needs and inquires. Our clients especially appreciate the particle counters and sizers allowing identification of drinking water treatment problems. The Streaming Current Monitors are a great tool for optimisation of expensive chemicals.”
Branislav
ECM ECO Monitoring - Slovakia
"Simply the best turbidity available."
John Clark
Chemtrac - Atlanta, GA
"In 2019, we purchased 29 particle counters which were installed in our water plants. So far, their performance has been perfect."
Li Yongjun
Jinan Hongquan Water Company - China
"We have installed hundreds of ozone analyzers from Pi over the years. They are just accurate, reliable and require low maintenance."
Jiao Tumei
Qingdao Guolin Environmental Technology Co., Ltd., - China
"Over the last few years we've purchased chlorine and turbidity analyzers from Chemtrac and with routine calibration the probes measure the chlorine and turbidity without any issue. We are very happy with this product and would highly recommend them."
Daniel "Buck" Owen
Ocoee Utility District - Ocoee TN
"We've been using these analyzers since 2008. They're easy to use and very stable. Calibration and maintenance is quick and simple."
Lloyd Gruginski
Chehalis WTP - Chehalis, WA
"The Pi products provide excellent value for money and represent the best municipal drinking water analyzers available."
John Clark
Chemtrac - Atlanta
“Servicing customers is much more than just solving problems or addressing complaints and Pi does that very competently with technical and quick efforts providing a good experience."
Clovis Tuchapski
Buckman - Latin America
"Pi's technical team has enabled us to be one step ahead of our competitors by adding value to our projects thanks to their fast and excellent support from the moment you first reach out.
Ibrahim Kaplin
Thermomed - Turkey
"Going from ORP control to amperometric chlorine sensor control has undoubtedly improved the pool water immensely!"
Chris Tedeschi
Link Automation - USA
"The Streaming Current Monitor from Pi is the best SCM I have ever used. The analyser responds quickly and has many powerful functions, which helps me save a lot of money."
Ye Yancong
Xiamen Xishan Water Plant - China
“Process Instruments has a broad range of high quality and user-friendly solutions for water-industry problems. The short lead times and great customer support make Pi a reliable partner.”
Péter Szabó
SC KATALIN NOHSE CHIMIST IMPORT SRL - Romania
"Process Instruments UK always have a high level of customer service. All our interactions with Pi have exceeded our expectations. It is always a pleasure working with you.”
Iñaki Seisdedos Rodríguez
Izasa Scientific - Spain
"The support from Pi and its partners is superb. They go above and beyond to ensure that, not only is their equipment perfect but that the process is working great too. Five Stars!"
Anthony Glitto
Equip Solutions - Illinois, USA
"Process Instruments UK always have a high level of customer service. All our interactions with Pi have exceeded our expectations. It is always a pleasure working with you.”
Rudi Tuffek
Allpronix - South Africa